Bulk material handling is the process of storing, transporting, and discharging various types of solid materials in powder or granular form. Bulk material handling is essential for many industries, such as food, chemical, pharmaceutical, mining, construction, agriculture, etc. However, bulk material handling can also pose many challenges, such as material flow problems, material degradation, segregation, or contamination, loss of storage capacity, energy waste, and production downtime.
One of the most effective solutions to overcome these challenges is to use bin activators. Bin activators are devices that attach to the bottom of silos or hoppers and create vibrations to fluidize the material and facilitate its flow. Bin activators can improve the flow of material by reducing the friction and cohesion between the particles, breaking down any potential arches or bridges, and promoting mass flow.
In this blog post, we will explain the benefits and applications of bin activators, as well as their design and operation principles.
Benefits of Bin Activators
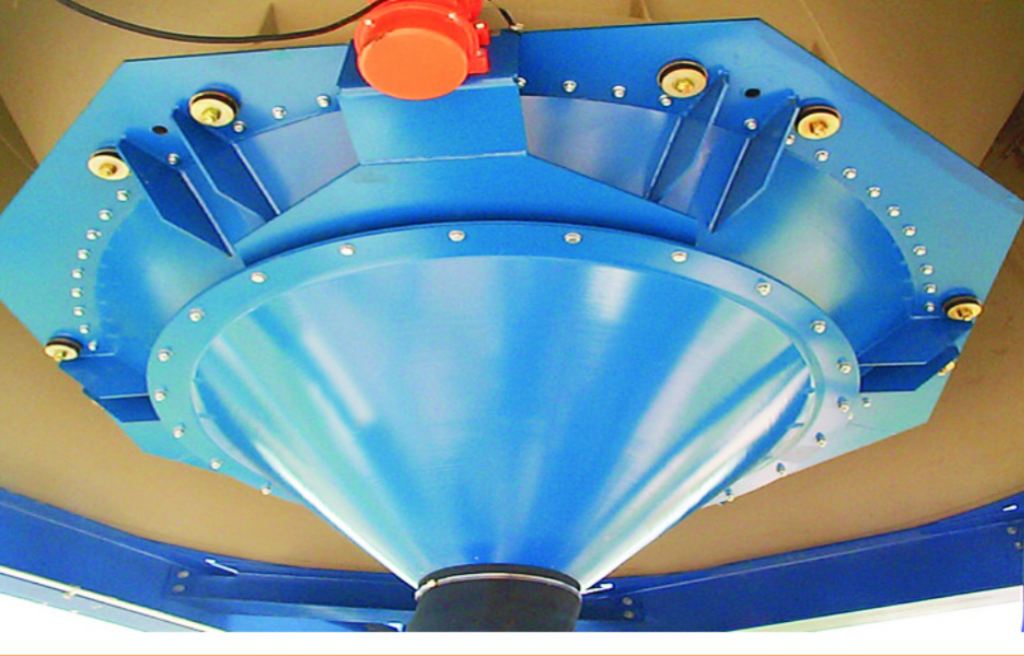
Bin activators offer several advantages over other methods of material discharge, such as pneumatic hammers, air cannons, or fluidized pads. Some of these advantages are:
- They provide a uniform and controlled flow of material, regardless of the material properties or the geometry of the silo or hopper. This means that the material is discharged at a constant rate and volume, without any fluctuations or interruptions. This can improve the efficiency and quality of your production process, as well as reduce the waste and downtime.
- They prevent the material from degrading, segregating, or contaminating, as they do not subject it to excessive force or air injection. Excessive force or air injection can damage the material structure, cause the material to separate into different fractions, or introduce foreign particles into the material. This can affect the material quality, performance, and safety. Bin activators, on the other hand, gently fluidize the material and maintain its integrity and homogeneity.
- They increase the storage capacity of the silo or hopper, as they prevent the material from compacting or bridging in the upper part of the structure. Compacting or bridging can reduce the effective volume of the silo or hopper, and cause the material to stagnate and spoil. Bin activators, on the other hand, keep the material loose and flowing, and utilize the entire volume of the silo or hopper.
- They reduce the energy consumption and maintenance costs, as they operate with a low power motor and have no moving parts or consumables. Other methods of material discharge, such as pneumatic hammers, air cannons, or fluidized pads, require high power and air consumption, and have parts that wear out or need to be replaced. Bin activators, on the other hand, have a simple and robust design, and require minimal maintenance and service.
Applications of Bin Activators
Bin activator can be used for a wide range of materials, such as flour, sugar, salt, cement, sand, coal, plastic pellets, animal feed, etc. They can be applied in various industries, such as food, chemical, pharmaceutical, mining, construction, agriculture, etc. They can also be customized to suit different sizes, shapes, and configurations of silos or hoppers, as well as different environmental conditions, such as temperature, humidity, pressure, etc.
Design and Operation of Bin Activators
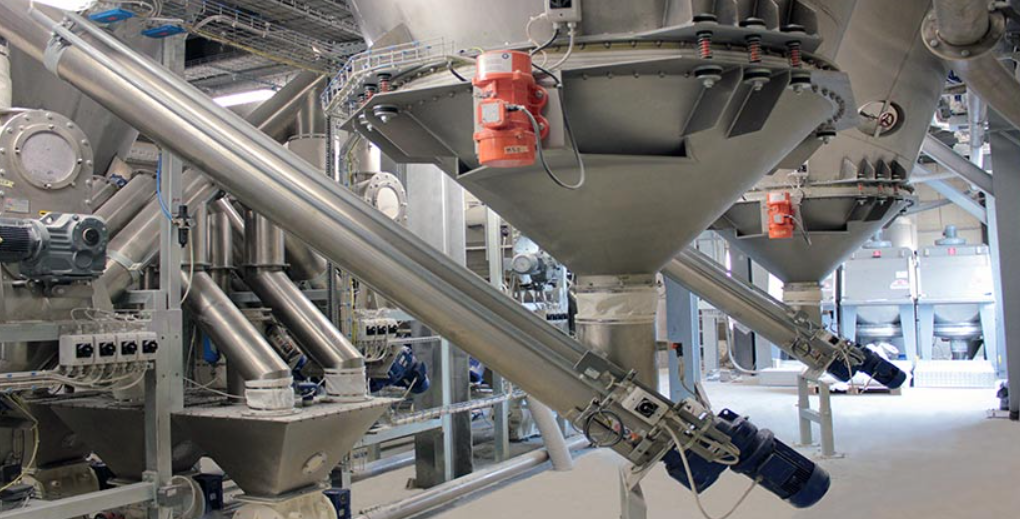
Bin activators consist of three main components: the cone, the seal, and the vibrator. The cone is the conical-shaped part that is attached to the bottom of the silo or hopper. The cone has a baffle plate at its center, which helps to direct the material flow and impart force to the material to break down any potential arches or bridges. The cone also has a secondary deflector plate below the baffle, which acts as a wedge to relieve the weight of the material from the lower part of the cone and push it around the areas near the cone surface.
The seal is the flexible connection between the cone and the silo or hopper. The seal is made of an engineered polymer that prevents the material from leaking and the cone from slipping off. The seal also isolates the vibrations from the silo or hopper, so that only the cone vibrates and not the entire structure.
The vibrator is the motor that generates the vibrations for the cone. The vibrator is housed in a single sealed enclosure, with no belts or oil to cause maintenance issues or contamination. The vibrator has adjustable eccentric weights that allow the vibration intensity and frequency to be changed according to the material characteristics and flow requirements.
The operation of bin activators is based on the principle of gravity and vibration. When the material comes in contact with the cone, it compresses and compacts the material before discharging it. The cone vibrates horizontally and vertically, creating a fluidized zone of material around the cone. The vibration also transmits force to the material in the upper part of the silo or hopper, as the movement propagates from particle to particle. As a result, all the particles flow freely in the bin activator towards its outlet. As long as there is no obstruction in the outlet, the material will be discharged from the bin activator.
The outlet of the bin activator is designed to be large enough to allow the material to flow without restriction. The outlet can be connected to various downstream equipment, such as screw conveyors, belt conveyors, pneumatic conveyors, etc. The bin activator can also be equipped with a slide gate valve or a butterfly valve to control the flow rate and stop the flow when needed.
Bin activators are effective and efficient devices that enable the smooth and reliable discharge of material from silos or hoppers. They have several advantages over other methods of material discharge, such as uniform and controlled flow, prevention of material degradation, segregation, and contamination, increase of storage capacity, and reduction of energy consumption and maintenance costs. They can be used for a variety of materials and industries, and can be adapted to different requirements and specifications.